I. Introduction
A. Importance of GMP Training in Manufacturing
GMP training ensures product quality, regulatory compliance, and consumer safety in manufacturing. It’s crucial for maintaining consistency and reliability. Without it, companies risk producing substandard goods, damaging reputation, and facing costly recalls. Investing in GMP training demonstrates commitment to quality and competitiveness in the industry.
B. Overview of GMP Training and Its Significance
GMP training educates personnel on principles, practices, and regulations governing manufacturing. It covers hygiene, documentation, equipment maintenance, quality control, and compliance. It’s essential for minimizing risks, improving efficiency, and ensuring product integrity in today’s competitive market. Effective GMP training fosters a culture of excellence and continuous improvement within organizations.
II. Understanding GMP Training
A. What is GMP Training?
GMP training encompasses educational programs designed to familiarize personnel with the principles and practices of Good Manufacturing Practices. It covers topics such as hygiene, documentation, quality control, and regulatory compliance.
B. Why GMP Training is Crucial for Manufacturing Industries
GMP training is essential for ensuring product quality, safety, and compliance with regulatory standards. It helps employees understand their roles and responsibilities in maintaining GMP standards, leading to improved efficiency and reduced risks of errors or contamination.
C. Regulatory Framework and Compliance Standards
GMP training familiarizes employees with the regulatory framework governing manufacturing operations. It covers relevant regulations and standards set forth by regulatory bodies to ensure that products meet quality and safety requirements. Understanding these standards is crucial for compliance and avoiding legal issues or penalties.
III. Benefits of GMP Training
A. Ensuring Product Quality and Safety
GMP plays a pivotal role in ensuring that products meet high-quality standards and are safe for consumption or use. By educating employees on proper manufacturing practices, hygiene protocols, and quality control measures, GMP training helps minimize the risk of product defects, contamination, or deviations from specifications.
B. Regulatory Compliance and Risk Reduction
One of the primary benefits of GMP is facilitating regulatory compliance and reducing operational risks. By familiarizing employees with relevant regulations, standards, and compliance requirements, GMP training helps companies adhere to legal obligations, avoid penalties, and mitigate the risks of non-compliance, such as product recalls or legal liabilities.
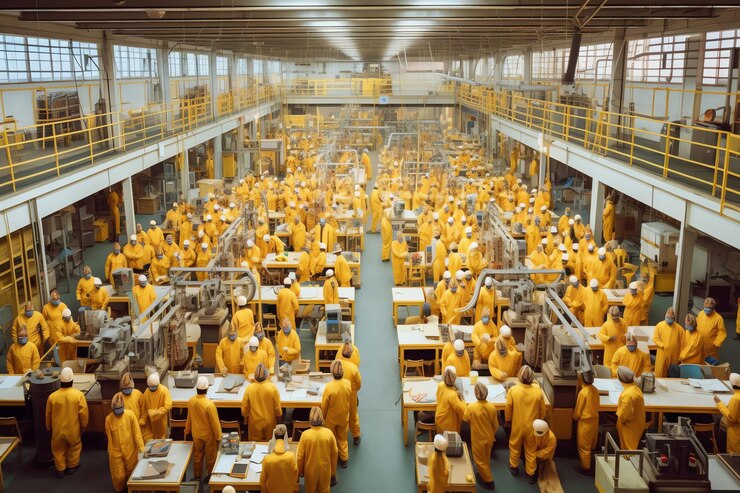
IV. Components of GMP Training
A. Hygiene and Cleanliness Standards
GMP covers hygiene and cleanliness standards essential for maintaining a sanitary manufacturing environment. This includes personal hygiene practices, cleanliness of facilities and equipment, and measures to prevent cross-contamination.
B. Documentation and Record-Keeping Practices
Effective documentation and record-keeping are integral components of GMP. Employees learn how to accurately document manufacturing processes, batch records, and quality control activities. Proper record-keeping ensures traceability, accountability, and compliance with regulatory requirements.
C. Equipment Maintenance and Calibration Procedures
GMP includes training on equipment maintenance and calibration to ensure equipment reliability, accuracy, and consistency. Employees learn how to perform routine maintenance tasks, calibration procedures, and equipment validation to minimize downtime and ensure accurate results.
D. Quality Control Measures and Inspection Processes
Quality control measures and inspection processes are fundamental aspects of GMP. Employees are trained to identify and address deviations from quality standards, perform inspections, and implement corrective actions to maintain product quality and compliance with specifications. This includes sampling, testing, and release procedures to ensure that only products meeting quality standards are distributed to customers.
V. Implementing Effective GMP Training Programs
A. Assessing Training Needs and Objectives
Before implementing GMP programs, it’s crucial to assess the training needs and objectives of the organization. This involves identifying gaps in knowledge or skills, understanding regulatory requirements, and determining specific training goals to address them effectively.
B. Developing Engaging Training Materials
Developing engaging and interactive training materials is essential for effective GMP. This may include multimedia presentations, case studies, role-playing exercises, and hands-on demonstrations tailored to the learning preferences and needs of the audience.
C. Choosing Delivery Methods: Online, In-person, Hybrid
Selecting the appropriate delivery method for GMP is essential to ensure maximum effectiveness and accessibility. Organizations may choose from various delivery options, including online training modules, in-person workshops, or hybrid formats combining both virtual and face-to-face instruction.
D. Evaluation and Continuous Improvement Strategies
Evaluation and continuous improvement are integral parts of effective GMP programs. Organizations should establish mechanisms to assess the effectiveness of training initiatives, gather feedback from participants, and identify areas for improvement. This feedback loop allows for ongoing refinement and enhancement of training content and delivery methods to ensure long-term success and compliance with GMP standards.
VI. GMP Training for Different Roles and Responsibilities
A. Target Audience: Production Staff, Quality Control Personnel, Supervisors
GMP is tailored to various roles within the organization, including production staff responsible for manufacturing processes, quality control personnel tasked with ensuring product quality and compliance, and supervisors overseeing operations. Each group receives specialized training relevant to their responsibilities and functions.
B. Tailoring Training Programs to Specific Job Functions
GMP programs are customized to address the specific job functions and requirements of different roles within the organization. This may involve focusing on particular aspects of GMP relevant to each role, such as hygiene practices for production staff, documentation requirements for quality control personnel, and leadership skills for supervisors.
VII. Best Practices in GMP Training
A. Promoting a Culture of Compliance and Quality
Promoting a culture of compliance and quality is essential in GMP. This involves instilling a sense of responsibility and commitment to GMP standards among employees at all levels of the organization. Emphasizing the importance of adherence to regulations and quality standards fosters a culture of accountability and ensures consistent compliance with GMP requirements.
B. Encouraging Active Participation and Engagement
Active participation and engagement are key to effective GMP. Encouraging employees to actively participate in training sessions, ask questions, and share experiences enhances learning outcomes and retention of information. Interactive activities, discussions, and case studies can help engage participants and make training sessions more dynamic and impactful.
C. Providing Ongoing Support and Resources
Providing ongoing support and resources is essential for reinforcing learning and promoting application of GMP principles in the workplace. This may include access to additional training materials, job aids, and reference guides to support employees in applying GMP practices in their daily tasks. Regular communication and feedback mechanisms also help ensure that employees feel supported and can seek assistance when needed.
VIII. Challenges and Solutions
A. Common Challenges in GMP Training Implementation
Implementing GMP may face challenges such as lack of employee engagement, limited resources, and resistance to change. Ensuring effective communication and understanding of the importance of GMP training can help address these challenges.
B. Strategies for Overcoming Training Barriers and Obstacles
To overcome training barriers and obstacles, organizations can implement strategies such as providing clear objectives and expectations, offering flexible training options, and incorporating interactive and engaging training methods. Tailoring training programs to address specific needs and challenges can also enhance effectiveness.
IX. Future Trends and Developments in GMP Training
A. Emerging Technologies and Innovations in Training Methods
As technology continues to advance, emerging technologies such as artificial intelligence (AI), augmented reality (AR), and machine learning are expected to revolutionize GMP training methods. These technologies offer interactive and immersive learning experiences, enabling employees to engage with training materials in new and innovative ways.
B. Integration of Digital Tools and Virtual Reality in GMP Training
The integration of digital tools and virtual reality (VR) technology is poised to enhance the effectiveness of GMP programs. VR simulations allow employees to practice real-world scenarios in a safe and controlled environment, improving retention and application of GMP principles. Digital tools such as mobile apps and e-learning platforms also offer flexibility and accessibility in delivering training content to employees.
X. Conclusion
A. Recap of Key Points: Importance of GMP Training for Manufacturing Excellence
In conclusion, GMP plays a crucial role in ensuring product quality, regulatory compliance, and operational efficiency in manufacturing. By equipping employees with the knowledge and skills needed to adhere to GMP standards, organizations can maintain consistency, reliability, and integrity throughout the production process.
B. Encouragement to Prioritize GMP Training Initiatives
We encourage organizations to prioritize GMP initiatives as a strategic investment in their long-term success. Investing in employee training not only enhances compliance and quality but also fosters a culture of continuous improvement and innovation, driving business growth and competitiveness.